The Tech
From desk tops to lap tops to smart phones, new platforms create a more pervasive and mobile network. The latest breakthrough is wearable technology for the Internet of Things. According to Goldman Sachs, the Internet of Things will drive the number of internet clients from 2 billion to 28 billion by 2020 1 . Driving this boom are smart fabrics: electronic textiles that carry data and conduct, reflect and absorb energy. Smart fabrics transform apparel and furnishings into the components of Personal Area Networks for connected cities, homes, vehicles and wearable accessories. They are now applied to everything from sensors, optical & electronic materials, actuators, space heaters, super- capacitors, antimicrobial textiles and even odor control. This paper will discuss how conductive polymer technology is leading to breakthroughs and exciting applications for smart fabrics now and in the future.
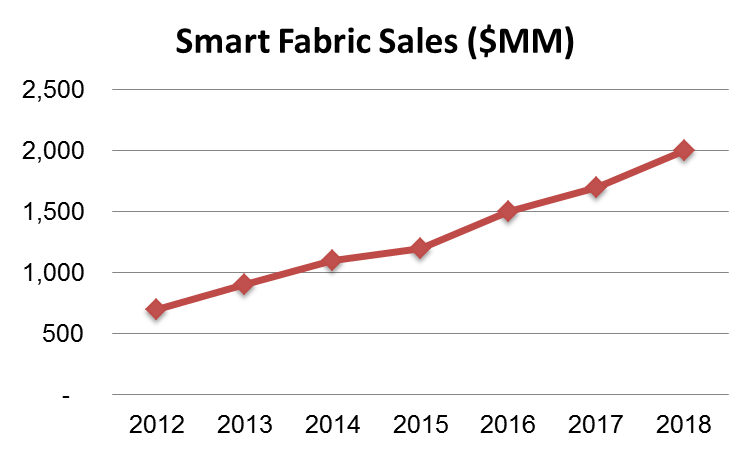
Among the more exciting developments, smart fabrics are solving technical challenges associated with wireless sensor networks. A U.S. National Research Council report said the use of wireless sensor networks throughout society “could well dwarf previous milestones in the information revolution”. Sources ranging from MIT’s Technology Review to Business Week have identified sensor networks as one of the top ten emerging technologies of the 21st century. Smart fabrics create textile sensors with 1 The Internet of Things: Making sense of the next mega-trend, Goldman Sachs, September 3, 2014. different functionalities. The fabrics also wirelessly connect the sensors and other network loads to power supplies for the secure transmission of energy and data.
Leading technology and fashion companies are jumping on board the smart fabrics opportunity. Google and Levi Strauss debuted Project Jacquard, a touch sensitive fabric integrated with an app. Ralph Lauren’s PoloTech shirt collects biometric data and streams it to a smart phone. Intel is putting the Intel inside— our clothes.
President Obama announced a new program to invest $500 million in public-private partnerships focused on cutting edge technologies and a new, textiles-focused manufacturing institute competition run by the Department of Defense. The intent is to improve the capabilities of small manufacturers through Manufacturing Extension Partnership competitions in twelve states. In April 2016, U.S. Secretary of Commerce, Penny Pritzker, will host the first Smart Fabrics Summit in partnership with the Industrial Fabrics Association International. According to her:
“Recent advances in technology have brought together the apparel, technology, and textile industries to develop new capabilities in fabrics with the potential to change how athletes, patients, soldiers, first responders, and everyday consumers interact with their clothes and other textile products.
“Known as ‘smart fabrics’, these new high-tech products have the capability to interact with their user or environment, including by tracking and communicating data about their wearer or environment to other devices through embedded sensors and conductive yarns.”
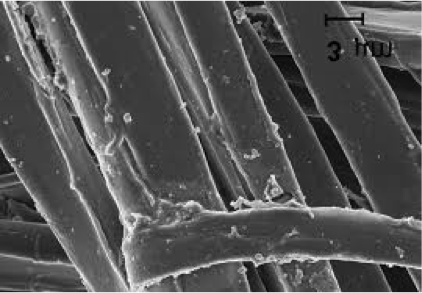
Alan Heeger, winner of the Nobel Prize in 2000 for the co-discovery of conductive polymers said that they are now “One of the top three fields of activity in condensed matter science,” based on publication and citation metrics. “It’s growing into a significant technology…[the] unique electrochemistry of these polymers … continues to be exciting and growing and…the last point I wanted to make is the discovery and development of transistors.
Heeger’s group is tackling transistors that he refers to as “the most important circuits of modern electronics…We’re studying polymer field-effect transistors with very high mobility, mobilities approaching 100cm2/Vs which gives me optimism that they will really be used in circuits for a wide variety of circuit applications,” he explains.2
Heeger is referring to the vision that conductive polymers will enable the creation of novel electronics whose circuits are engineered at molecular scale—over a hundred times smaller than what has been achieved with silicon.
As the Royal Swedish Academy of Sciences who awarded the Nobel concluded:
The dream is thus to put electronic circuit properties into single molecules. Arrays of such molecules – possibly connected by conductive-polymer wires – on molecular scaffoldings would form molecular wafers. One may speculate that reduced dimensions from 200 nm to, say, 2 Å, and the concomitant shrinkage in circuit size could increase the speed and dynamic memory of computers by a factor of 108. Such progress would correspond to forty years of computer technology development. Conductive polymers may become crucial for the building of such a molecular electronics world.
Eeonyx Corporation’s former CEO, Jamshid Avloni, and current CTO, Mahemuti Abula, worked in concert with Heeger’s fellow Nobel recipients, Alan MacDiarmid and Hideki Shirakawa, respectively.
While this vision of molecular scale electronics remains to be realized, conductive polymers are leading the development of innovative materials. Thus far, dozens of different conductive polymers have been identified. Depending upon the combination and concentrations of polymer, dopant and catalyst, polymers may be tuned to deliver a gradient of conductivity ranging over several orders of magnitude and exceeding the conductivity of semiconductors, such as silicon. A gradient of tunable conductivity enables the engineering of materials that absorb as well as reflect energy; this energy absorbing capability is the stealth technology that protects aircraft and antennas from unwanted detection.
For smart fabric applications, conductive polymers offer unique advantages and properties compared to other conductive materials, such as metals and carbon loaded products. Conductive polymers weigh 1.5 grams per cubic centimeter, less than 1/8th-1/10th the weight of metals. Coatings have a thickness of a few microns. The amount of material in the coating will usually not increase the mass of the fabric by more than 1%. By contrast, with carbon loaded materials, the weight increase can be more than 30%.
Unlike metals and carbon loading, conductive polymers do not significantly affect the weight, drape and feel of the smart fabric.
Conductive polymers have synergistic interactions with other conductive materials. CP films provide metals with corrosion resistance and the ability to absorb as well as reflect energy for electromagnetic interference (EMI) applications. CP films increase the conductivity of carbon particulate and carbon nanotechnologies while carbon particles improve the ability of CP films to withstand high temperatures.
Because CP films are easily processed at ambient temperature and pressure, they are a lot cheaper than other conductive materials. The affordability of polymers is moving smart fabrics out of mission critical applications for first responders and healthcare and into the mainstream consumer market.

For example, the palms of these gloves are treated to create a capacitive charge. This charge allows the wearer to operate touchscreen devices– normally not possible with conventional gloves.
By integrating smart fabrics with other electronic components, it is possible to create integrated and networked products that measure the user’s performance and interact with the environment.


This glove measures pressures in discrete zones on the hand in order to help design robots with a sense of touch.
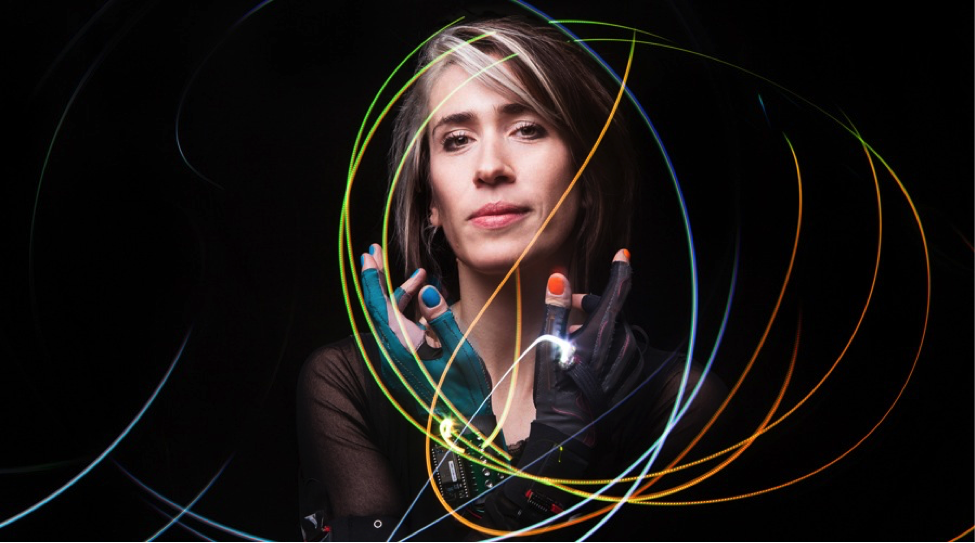
This Mi.Mu glove combines stretch sensing smart fabric with smart phone components and haptic feedback, allowing an artist to control synthesizers and lighting effects with hand gestures.

The development of wearable technologies still faces a variety of technical challenges. Electronic components are not easily integrated into garments; they do not wash and wear. They’re not very fashionable. Devices compete for power and bandwidth. People would prefer not to wear wires and carry battery packs.
Smart fabrics are helping to dissolve the difference between a garment and a gizmo. They also provide new opportunities for the wireless transmission of energy and power. By wireless networking a system of sensors, power supplies and other devices, the smart fabrics make it possible to relieve many of the power management issues associated with wearable technologies.
Eeonyx is pioneering the development of state of the art sensors. These piezo-resistive materials change their voltage in response to mechanical and chemical stimuli. They are first and only ultra- thin, wearable smart fabric sensor that measures all aspects of physicality: pressure, bend, stretch, and torsion. Millions of Eeonyx sensors are currently in use, even after years of rugged service. As small as 2mm in area x 0.25mm thick, Eeonyx’s sensors can be shaped to any geometry. The dynamic range of any one sensor is 1:2,000, accurately and uniformly measuring forces.
The fabrics may be used as on/off switches and they map motion over the surface of the fabric in the x, y, and z axes.
They can be augmented with printed circuits made from stretchable conductive inks to create discrete zones of force measurement within a sensor. Eeonyx sensors are used in industry for product design and package testing as well as in complex products including:
- MIDI controllers
- Robotic exoskeletons
- Athletic socks, shoes and bicycle pedals
- Hospital beds
- Wheelchairs
- Auto parts
- Industrial safety mats

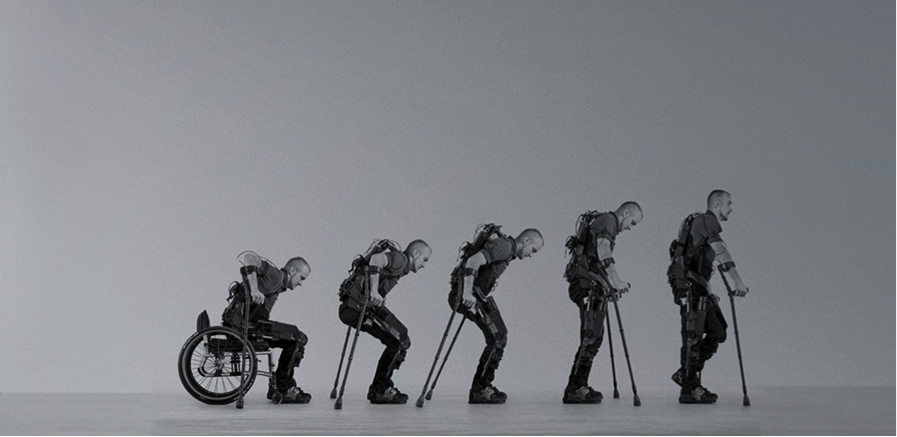
The Eeonyx sensors set the industry benchmarks for linearity, homogeneity, hysteresis and static drift.

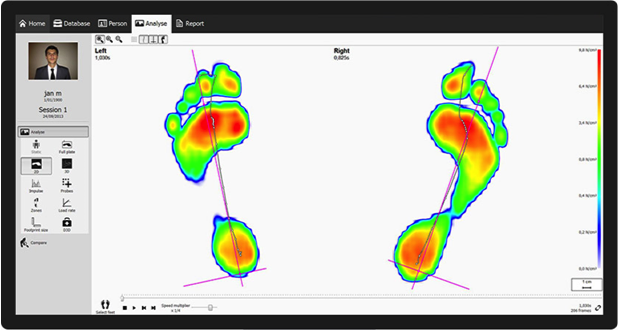
As shown above, customers use Eeonyx sensors to acquire fine grained data from multiple simultaneous touchpoints for sophisticated analysis and to actuate devices.
Within the MIDI controller, sensors eliminate dials and sliders. After integration with connectors, microcontrollers or CPUs, the MIDI controller maps pressures on the key pads to create sounds that mimic the vibrato of stringed instruments.
The RsScan treadmill tracks footsteps in real time to improve shoe sizing, selection and the design of orthotic appliances.
Networks of distributed sensors face technical challenges because they rely upon wired transmission of electric power and low power wireless communication through free space. Eeonyx’s novel network addresses these challenges by wirelessly conducting a magnetic field across the surface of magnetically conductive materials. This field is also a sensor and can be monitored to detect intrusion.
There are still technical challenges concerning the limitations and vulnerabilities of sensing and communicating through free space. For military use, survivable and secure networks need a low probability of detection, interception and interference. The hardware and transmissions of over the air technologies are difficult to conceal and protect. Dense networks are also at risk of friendly electromagnetic interference (EMI). Networks need to be resource efficient. Broadcasting in three dimensions, free space transmitters lose energy and signal quality in proportion to the square or cube of transmission distance. They experience negative shadow fading and ground effects. The radiating infrastructure of antennas and dishes presents deployment challenges in rugged spaces, underwater, on vehicles and warfighters’ uniforms. It conspicuously attracts hostile fires.
- Low probability of network detection, interception and interference
- Minimized electromagnetic interference (EMI)
- Electrostatic dissipation (ESD) and EMI shielding and absorption
- Efficiency is proportional to distance (1/d) rather than distance squared (1/d2)
- Elimination of shadow fading and ground effects
- Multifunctional piezo-resistive textile sensors
- Light, flexible components for rapid deployment in spaces, vehicles and clothes
- Economical manufacture of network components
Proof of concept demonstrations of the network achieved data transfer of 10,000 kbps over tens of meters with 10mW of power. With 1 watt of power the range of energy and data transfer increased to several hundred meters. It is anticipated that the area of the network could be extended to a square kilometer with higher energy input.
Current research is focused upon creating an asynchronous network with a small array of devices deployed in an area of 2,500 square meters. The objective is to characterize performance on and off the conductive pathway as a function of distance and injected power. Thereafter, the goal is to map the baseline of the magnetic field’s spectral signature and to evaluate perturbations in response to intrusive persons and vehicles. Following these measurements, the Eeonyx team plans to create larger networks within an area of one square kilometer.

Eeonyx has developed a novel system to meet these challenges. The technology minimizes free space transmission. Instead, a magnetic field is injected into the conductive surface of a metamaterial that is the backbone emitter for the wireless transmission of energy and data between energy sources, multifunctional sensors and permitted users.
This metamaterial backbone also creates its own magnetic field. The field has a reflected standing wave which can be monitored to detect intrusion within the smart space of the network. As an intruder approaches the field’s point of injection, the field is stretched and perturbed. The spectral sweep differentials provide data for analysis and identification.
The thin flat fabrics of the system are discreet and difficult to detect. Beyond the point of injection, its magnetic field is undetectable in free space. The network is not obstructed by objects and can “see” through walls. A magnetic field is difficult to disrupt and is not affected by EMI. The Eeonyx metamaterial prevents EMI and provides a low radar cross section. Signal strength declines in proportion to distance rather than the square of the distance. The metamaterial is light weight, and easily conforms to irregular shapes.
The sensors, emitters, connectors, circuits and encapsulation materials can be made of textiles and produced at industrial economies of scale with textile manufacturing technologies. Textiles are easily cut and sewn into clothing for wearable Personal Area Networks.
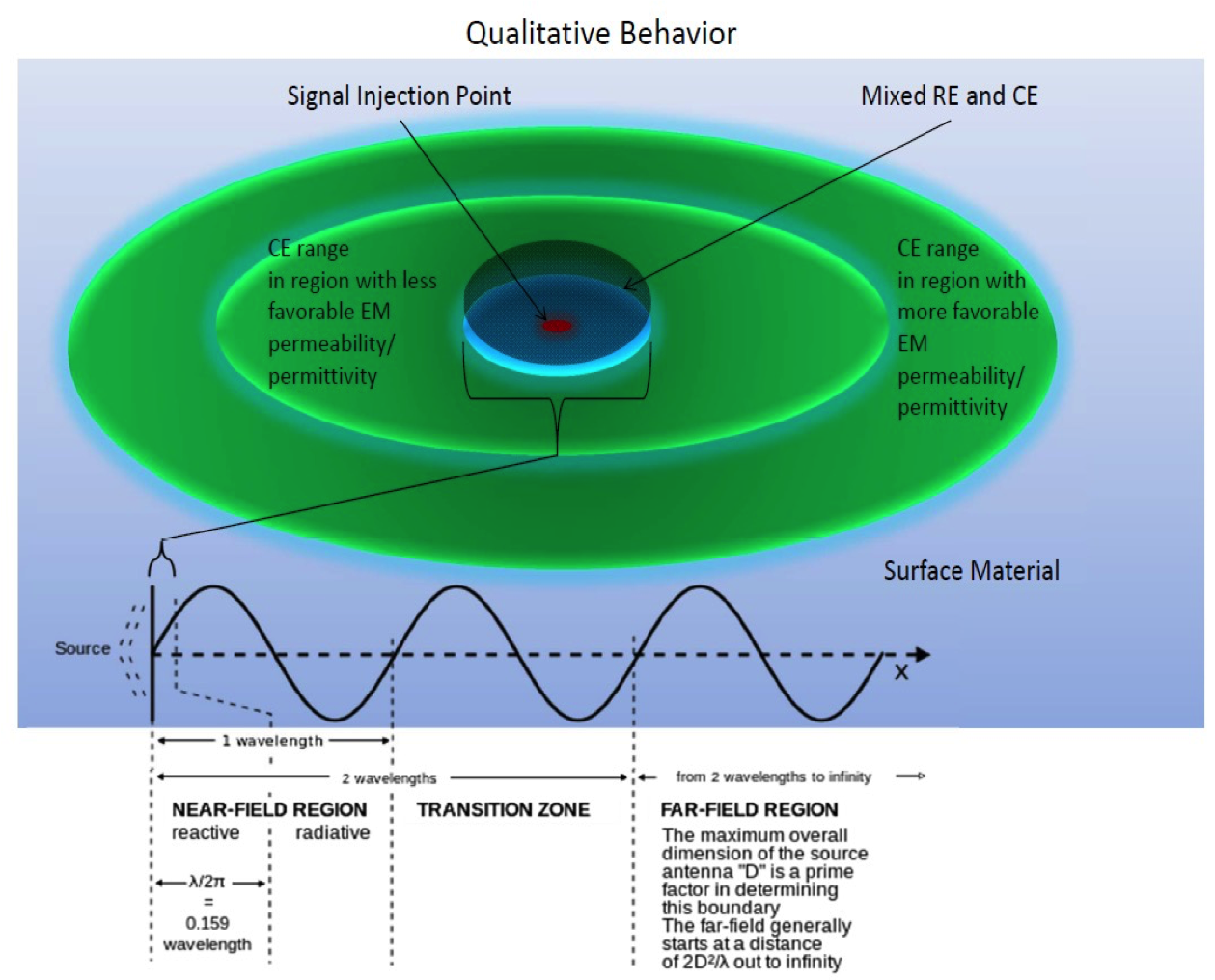
The backbone of the system is the metamaterial emitter. The emitter shows negative broadband permittivity at frequencies above 4.5 GHZ. This property causes the material to be a lossy conductor of electric portion of an electromagnetic field. With permeability just above 1, it is a superior conductor of magnetic fields.

Because of the material’s effects upon electrical fields, it is used in defense applications for stealth, EMI shielding and static dissipation. Products with sheet resistivity in the range of 10-200 Ohms per square reflect, scatter and absorb EMI and provide shielding effectiveness ranging from -10 to -60dB.
The magnetic field emitter is a fabric or tape coated with a thin film of intrinsically conductive polymers. The conductivity of the polymer coating can be tuned: current products have a sheet resistivity ranging from 101-106 Ohms per square. For stealth applications, Eeonyx exploits this tunability by making edge cards with a tapered gradient of conductivity.
Conductive polymers have introduced a new class of semiconducting materials that are especially well suited to the creation of smart fabrics for wearable technologies. Recent developments in polymer technology has both improved the performance and lowered the cost, making it feasible to introduce wearable technologies to the mass consumer market. While wearable technologies still face technical challenges to the realization of wireless personal and area networks, new smart fabrics are offering elegant textile sensors and a new method for the wireless transmission of energy and data over the surface of fabrics.